Materials
A basic understanding of the materials used in the thermoforming process, and the capabilities and benefits of each, is an important part of servicing our customer’s needs. Each project needs to be reviewed from the standpoints of functionality, cost, aesthetics, as well as durability in shipping and at retail. Over time, material popularity waxes and wanes, dependent on the needs of the marketplace. Throughout the 90’s, PVC was the material of choice, based on cost and function. Currently, RPET is the most common material we process, but we also process PVC, HIPS, PETG, PLA, PP, and ABS, as well as different grades and specifications of those materials. Below is a basic primer on the different materials we handle most frequently.
PP (Polypropylene)
Of all the thermoform grade materials, Polypropylene has the poorest melt strength, which poses processing issues with the type of wide bed machines that we use. Excessive sheet sag can cause noticeable gauge variances, as well as webbing issues in the formed part. In addition, PP displays significant shrinkage during processing, which makes it a challenge to maintain flange and part concentricity. Due to these factors, choosing this material requires greater consideration of the tooling design, and requirements of the formed part. Polypropylene displays superior impact resistance, and is well suited to applications such as dunnage trays. The material is very flexible, but is not well suited to tight tolerance parts, where structural rigidity is a benefit. PP processes much slower than any other material Blisters run, which can have a marked impact on part cost. PP is as 'recyclable' as most other materials, but is not considered to be an ecologically beneficial material choice. Blisters can process PP in gauges from 15 mil to 60 mil.
ABS (Acrylonitrile Butadiene Styrene)
ABS is a blend of acrylic and styrene, yielding a material that is significantly stronger than standard HIPS, with a glossy appearance, and great impact resistance. Raw material cost can be nearly double that of HIPS, and it processes at a slower rate, which also impacts finished part cost. Trays requiring superior structural rigidity due to product weight, are a good application for this material. Recyclability is similar to HIPS. Blisters can process ABS in gauges from 15 mil to 45 mil.
PLA (Poly Lactic Acid)
PLA, is a cornstarch based material, which is biodegradable when composted. This material is incredibly brittle, even under the best conditions. If a package is designed to accommodate PLA, it is possible to create something that could survive the retail atmosphere, but the material could never be called impact resistant. In addition, the material softens above temperatures of 110 degrees, which requires it to be shipped in temperature controlled trucks, adding to shipping costs. While Blisters has run the material in the past, we do not recommend it for the types of packages we produce. The point also must be made, that since garbage is almost exclusively put into cap and fill landfills, PLA will not degrade in this type of environment. Oxygen is a critical component in the degradation of PLA, and these types of landfills are anoxic.
PVC (polyvinyl chloride)
PVC is considered to be one of the most impact resistant materials, with good formability, excellent clarity, and good cost to benefit ratios. Most virgin PVC has a slightly bluish tint to it, whereas recycled PVC can have a slightly grayish or greenish tint, due to contaminants in the scrap material used in processing. It is also available in custom colors, both translucent and opaque, although any colored material is subject to minimum order quantities. During processing, PVC sheds its heat more slowly than other materials, which results in slower cycle times, especially in the heavier gauges. PVC is the most easily sealed of the most common thermoform materials, with heat seal, RF, Sonic, and UV glue sealing all being options. PVC is susceptible to degradation from solvents, or other chemicals. Because it contains chlorine, PVC is viewed as being less ecologically friendly than most other thermoform grade materials, although it is every bit as recyclable as most other materials. We can run PVC in thicknesses ranging from 7.5 mil to 60 mil, although gauges thicker than 30 mil are difficult to source.
PET (Polyethylene Teraphthalate)
PET is currently the most common material we process, although the greater majority of that material is recycled, or RPET. Cost is the major driving force towards this change, although the lack of chlorine in the polymer is also a determining factor in the selection of this material. PET is probably one of the most rigid materials being used in thermoforming today, although that rigidity comes at the expense of impact resistance. RPET in particular can be prone to fracture in colder conditions, such as can be experienced during shipping in the winter. This rigidity also makes the material more difficult to cut in processing, compared to most other materials. Clarity is considered to be superior over other clear materials, even when using RPET. PET is also available in colors, but in a much more limited range. Formability compared to PVC is slightly reduced, particularly when forming a part with great detail. PET cools more quickly than PVC, and thereby processes at slightly higher rates, especially in the heavier gauges. PET is very difficult to seal. Although some processors have had limited success with Sonic welding, UV glue is the most consistent performer for this type of material. PET is chemically resistant to most solvents, and is frequently used for paint trays and other similar applications. Due to the absence of chlorine, PET is considered to be more ecologically friendly than PVC, and is more widely recycled, due to the large volume of 2 liter soda bottles being processed with the material. We can run PET in thicknesses of 7.5 mil to 35 mil.
PETG (modified Polyethylene Teraphthalate)
PETG is a chemically modified derivative of PET, which results in an ethylene glycol by-product that lowers the melting point of the material. This results in a material that more closely resembles PVC in impact resistance, process-ability, and in fact allows it to be sealed in similar ways to PVC. The major drawback to this material is cost. Virgin PETG can cost as much as 70% more than virgin PET, which limits the practical applications for this material. However, recycled PETG, or RPETG, has been a viable option for many customers with the need to heat or RF seal their packages, albeit at a greater cost. There are also co-extruded material solutions, with a thin outer layer of PETG, sandwiching a core of PET. This allows the material to be sealed in greater variety of methods, at a more viable price point. From an ecological standpoint, PETG is viewed similarly to PET. We can run PETG in gauges from 7.5 mil to 35 mil.
|
|
HIPS (High Impact Polystyrene)
In most cases, HIPS is utilized as a low cost, utility grade material. Although the raw material cost per pound is typically higher than PVC or RPET, the yield on the material is greater than either of those materials. Despite its name, HIPS can be prone to fracture, particularly on parts with high forming stress in them, such as deep draw parts. To combat that, we order material with an additional 5% of rubber modifier, to improve impact resistance. HIPS is available in both virgin and recycled (utility) grades, and any color a customer could possibly want, including metallic, and high gloss co-extruded finishes. From a processing standpoint, HIPS is probably the easiest, and most efficient material we produce. Cycle times, particularly in the heavier gauges, can be 15-30% higher than PVC or PET, and cutting is much easier. HIPS is recyclable, although it’s not viewed to be as ecologically friendly as PET. In terms of sealing, we’ve never had a project that was run on HIPS that required sealing, but HIPS will not seal to itself. HIPS is also easily affected by solvents, so it’s possible that UV glue might even pose a problem for the material. We can run HIPS in gauges of 10 mil to 60 mil.
Biodegradables
There has been quite a bit of interest in biodegradable packaging materials, but it’s important to understand that the term biodegradable can be a misnomer, as some materials that are advertised as such, are anything but (such as PLA). There is a big difference between being recyclable, and biodegradable. Once again, Blisters is working with an innovator in the field of biodegradable plastics, and are excited to offer a true bio-resin. Call Blisters to learn more!
Specialty Materials
In addition to the standard spec materials that we run, most materials are also available with different specialized properties. Not all types of materials are available in these configurations listed below.
FDA (Food and Drug approved materials)
This specialized material is used when the thermoform comes into direct contact with food products, or in some medical grade packages.
ESD (Electrostatic Dissipative material)
This type of material is specially treated to dissipate the static charge that builds up on plastic packaging. This material is used in the manufacture of packaging for sensitive electronic components, where a static charge could potentially cause damage to the product. Parts formed with ESD materials are subjected to additional quality control measures, being scanned with a meter that can measure the static charge on a given part. A log is created, and submitted along with the production order.
COEX (co-extruded material)
This is a broad definition of a type of material that has more than one layer of dissimilar materials extruded together. Co-extruded sheet can be as few as two layers, or as many as seven, depending on the application. An example would be co-extruded HIPS, with a utility base layer, and capped with a crystallized high gloss layer. This material is simply an aesthetic choice, and frequently used for POP displays or game trays. This is the most common type of COEX material we currently run.
Within the industry, co-extruded films are frequently used as a barrier material, to prevent transmission of odor or taste through the formed part. Some COEX barrier materials can have as many as seven layers, to accommodate different performance needs of the finished product.
PCR (Post consumer recycled material)
Most recycled materials that we process are in fact post industrial scrap, utilizing waste trim in the extrusion process at the sheet manufacturer, as well as trim scrap from thermoformers who sell the scrap back to the processor. PCR is a certified material that contains a specific amount of post consumer scrap, available in either 25% or 50% content. This type of material is commonly requested for use in specific areas such as California, where regulations require a given amount of post consumer waste included in packaging.
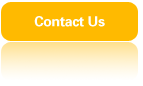
[ top of page ] |